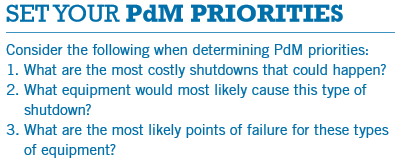
Avoid expensive equipment failures and loss of production capacity and keep your facility operating at peak efficiency by utilizing Predictive Maintenance (“PdM”) strategies. The ultimate objective of a sound maintenance program is to allow a convenient cost effective scheduling of corrective maintenance with the goal of preventing equipment failures prior to affecting production, quality or safety issues. This is accomplished by evaluating equipment condition by either periodic or continuous equipment monitoring.
AMSEnergy can provide services or training to set-up a complete predictive maintenance program that will save your site downtime and energy costs. Other costs savings that should be considered are those of increased equipment life time, environmental impacts, spare parts planning and the substantial savings of having the capacity to plan and schedule maintenance work as opposed to being completely reactionary.
Our predictive maintenance technicians are trained, certified and well known in their respective fields.
AMSEnergy can provide these services or training to your facility:
Effective for spotting both mechanical and electrical failures by reviewing the equipment’s heat signatures.
• Loose electrical connections
• Overheated transformers, motors, bus plugs, etc.
• Overheated bearings, linkages, sheaves
• Malfunctioning steam traps
• Building envelope integrity
• Faulty HVAC systems
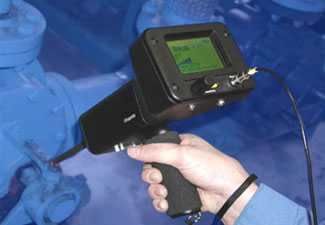
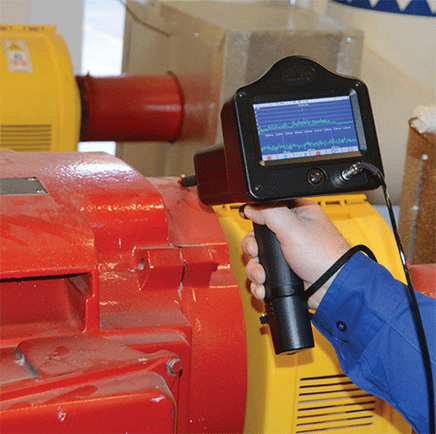
Ultrasound Technology
Effective for “hearing” problems in equipment by being sensitive to high-frequency sounds that are inaudible to the human ear and has the ability to discern them from lower-frequency sounds and mechanical vibrations. Ultrasound – literally “beyond sound” – refers to acoustic (sound) energy in the form of waves with frequencies above 20,000 Hz, the highest frequency to which the human ear can respond. In addition to its use for predictive-maintenance purposes, ultrasound has many other industrial uses, especially in processing applications. These include
• friction and stress in rotating equipment
• piping systems including steam, air and gases
• differentiate between normal and abnormal wear
• imbalance conditions
• electrical noise including transformers, sub-stations and disconnects
• Cleaning of equipment and process material
• Cutting
• De-foaming
• De-gassing
• De-scaling of plant equipment, evaporators, or pipework
• De – watering/ drying
• Extrusion
• Fermentation
• Filtration
• High – shear mixing
• Liquid/solid separation and dispersion
• Nanotechnology
• Particle de-agglomeration
• Sieving
• Spraying/spray drying/atomization
• Waste/sludge effluent treatment
• Welding
Tribology (oil analysis)
Effective for determining how surfaces are interacting – “wear”. This technology, when implemented properly, can be more predictive than other technologies.
• Effects of lubrication and additive properties
• Analysis of contaminants
• Hydraulic systems
• Gear boxes
• Machine slides
• Motor housings
• Friction in mating surfaces in equipment
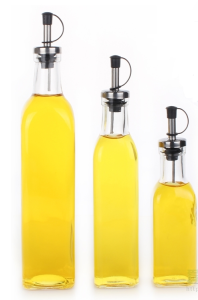
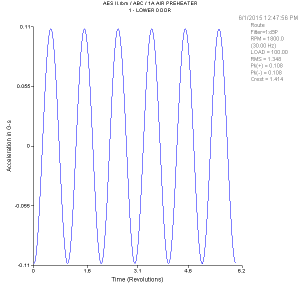
Vibration Analysis
The most sophisticated technology and is most productive on high-speed rotating equipment.
• Motor shafts and bearings
• Study of harmonics in equipment
• Structural dynamics
• Machine balancing
• Process critical speeds
Motor Circuit Analysis (MCA)
Identifies defective motors and their circuits prior to reaching catastrophic or functional failure.
• Locates faulty electrical connections in the motor circuit
• Test of windings and insulation properties
• Examine “rebuilds” for integrity
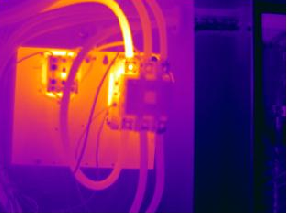